Home / Warehouse Consultants / Operations Management
Warehouse Operations Management
Here to reduce waste and improve profitability in your warehouse operations
INTRODUCTION
Reduce waste, improve profit
Warehouse operations management requires a systematic and process driven approach to maintain order and efficiency within a warehouse or distribution centre. Well designed operational processes can improve profitability, reduce waste and facilitate improved management of variability.
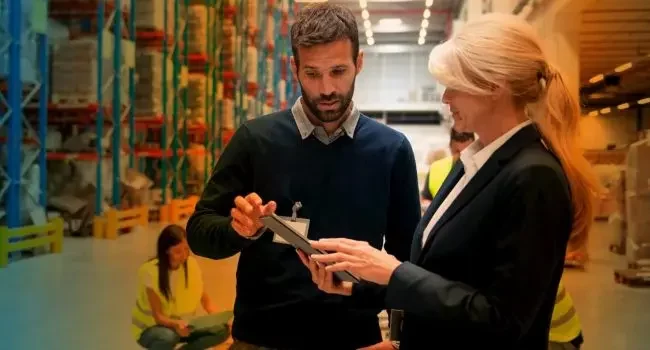
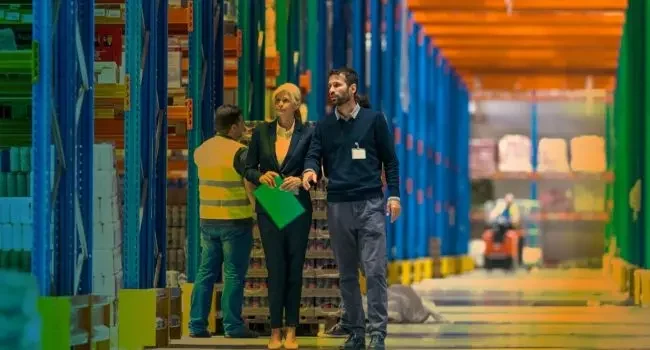
WAREHOUSE OPERATIONS MANAGEMENT
Process driven warehousing
Within warehouse operations management the focus for operational process improvement is on the efficiency of moving material and the utilisation of resources such as people, handling equipment and facilities. The material movements and utilisation must also be balanced to the service level requirements. All warehouse operations should look to continuously monitor and improve efficiency in order to control cost and deliver the required service.
CLIENTS
Who we work with
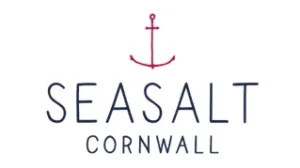
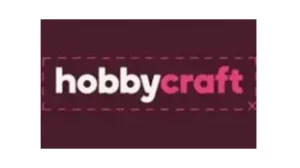
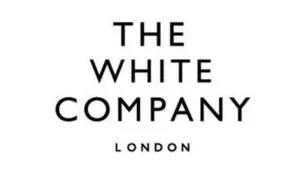
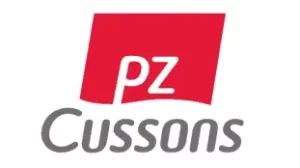
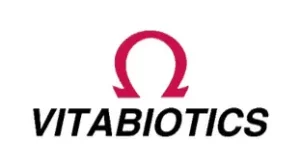
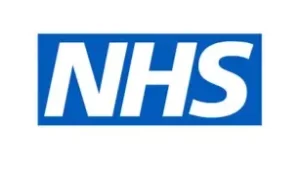
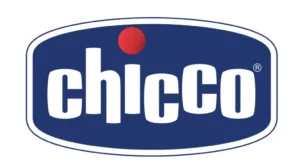
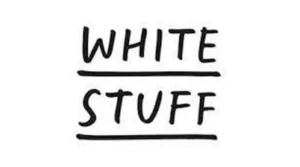
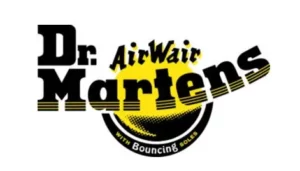
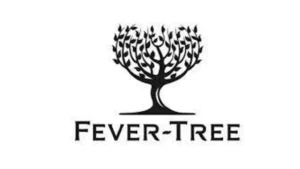
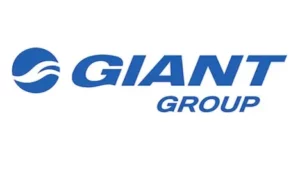
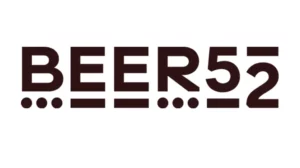
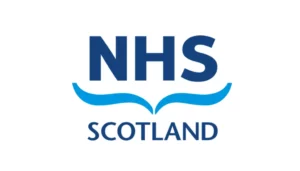
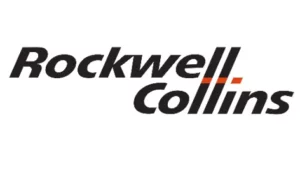
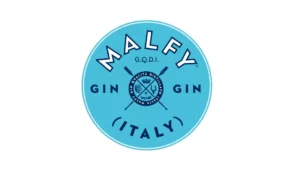
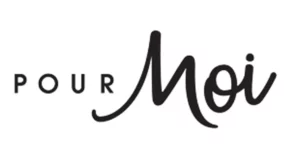
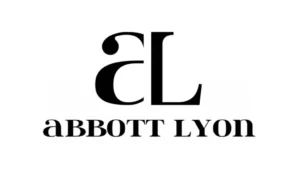
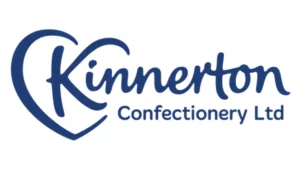
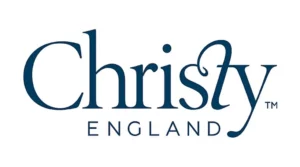
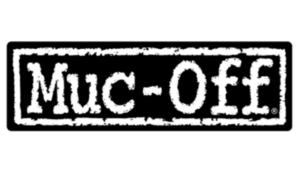
HERE TO HELP
Analysis and pragmatism
Developing efficient operating processes requires fact-based analysis combined with a pragmatic appreciation of business constraints. Whilst there are numerous different methodologies including Kaizan, Six Sigma, TQM and variations thereof, they all focus on a core approach; continuous focus on being organised, methodical and efficient.
Our warehouse consultants are technically skilled in the assessment of processes using a range of methodologies. They also bring considerable knowledge of the realities of day-to-day warehouse operations, gained through direct experience in managing logistics operations.
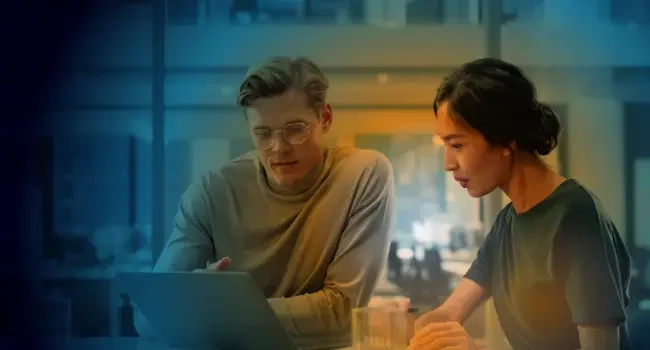
SERVICES
Warehouse operations management services
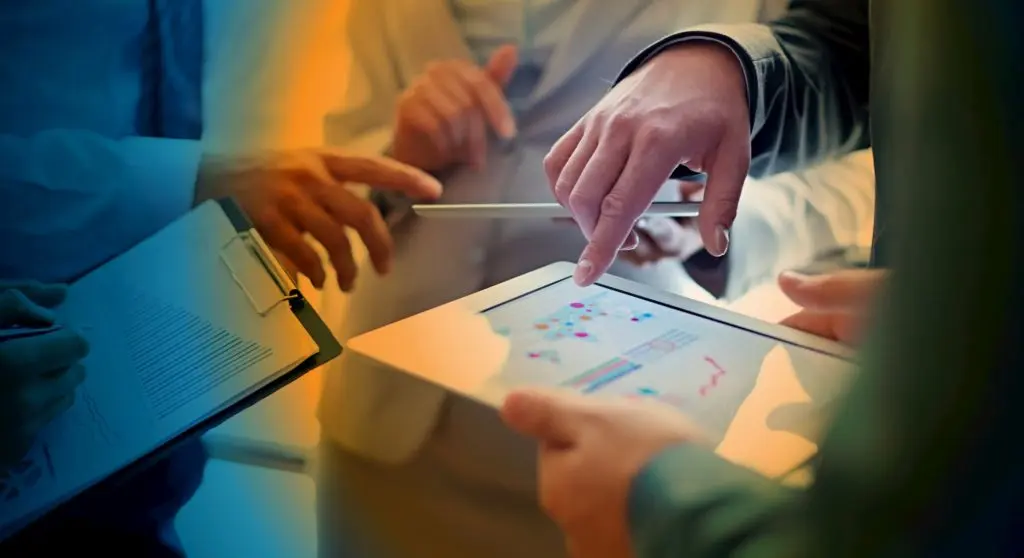
Cycle Time Reduction
Cycle time in the warehouse is the total elapsed time taken to complete a process, such as putaway of goods, order picking and pick-face replenishment.
In many warehouse operations the actual processes followed by personnel demonstrate a wide range of counterproductive and non-value add actions. Identifying and eliminating these actions is a major opportunity for service improvement and cost reduction.
Using appropriate elements from Lean and other process control methodologies, our team can map the existing processes, identify opportunities for improvement, develop recommendations and support clients with the implementation of those recommendations.
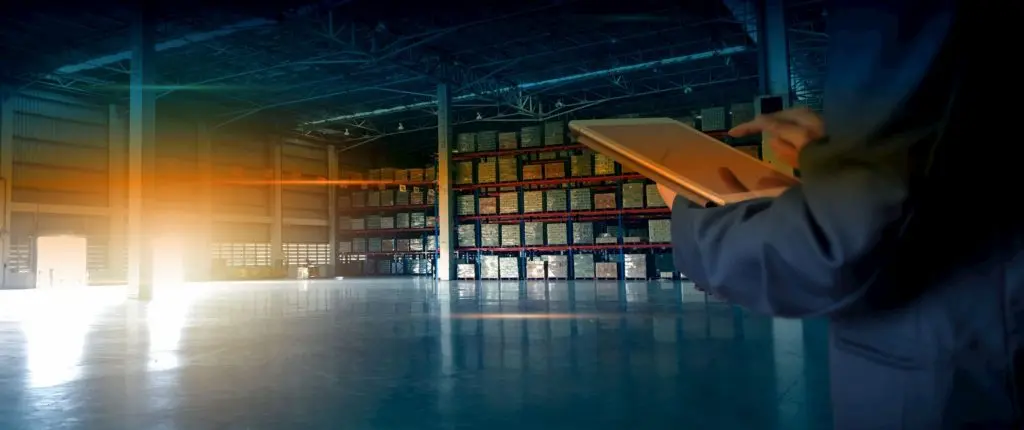
Warehouse Layout Improvement
All warehouses, regardless of the velocity of material movement, require an efficient layout. The layout of racking, pick routes, walkways, marshalling areas and loading bays are a key driver for the cycle times associated with warehouse activities. Further to the layout, the location of material within the layout is also a critical factor in ensuring cycle times are efficient.
Our warehouse consultants are able to optimise an existing layout through detailed modelling, and they are then able to generate full CAD schematics and equipment requirements to support the implementation of any required changes.
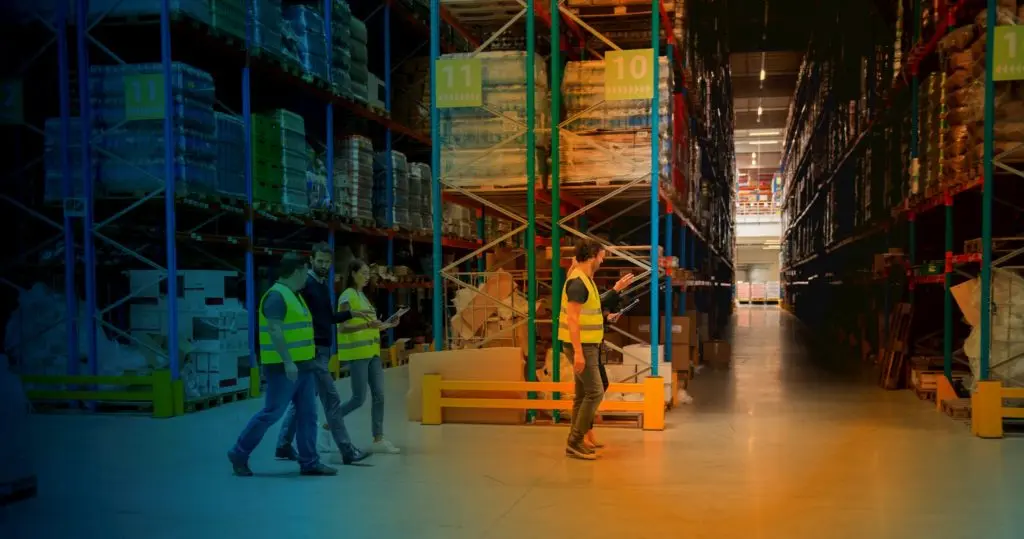
Inventory Reduction
It is not just working capital that over-stocking ties up, but also space. Reducing inventory, whilst balancing inventory levels with the level of product availability required, is a key element in ensuring that the space within a warehouse is efficiently utilised.
Our consultants can undertake a full review of inventory, establishing the optimum levels required and designing new inventory policies to ensure the optimum levels are achieved and maintained.
INSIGHT
Warehouse management articles & advice
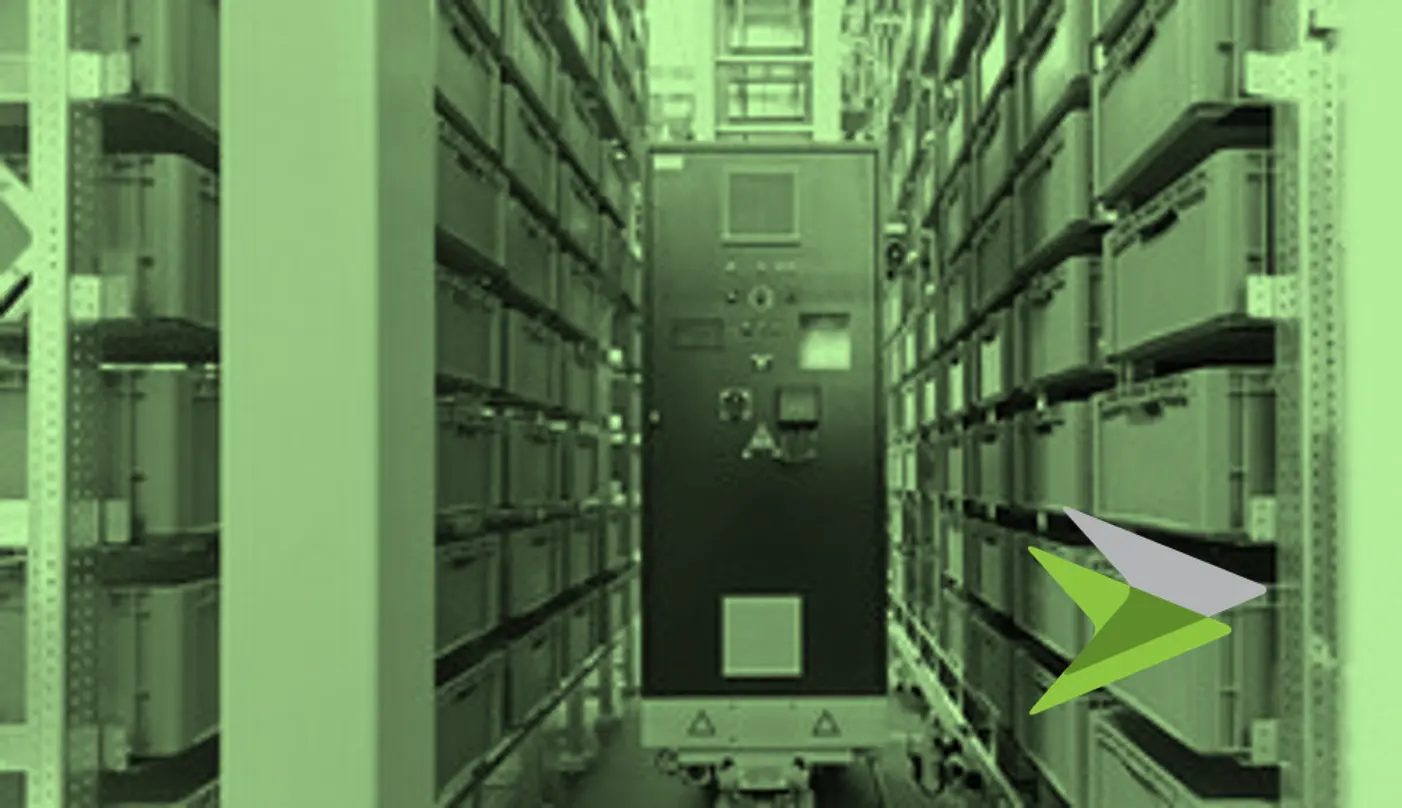
Food and Drink Warehousing: The Increasing Need for Automation
Automation is becoming the name of the game in warehousing, but in some instances, it is needed more than in others. Two primary factors are
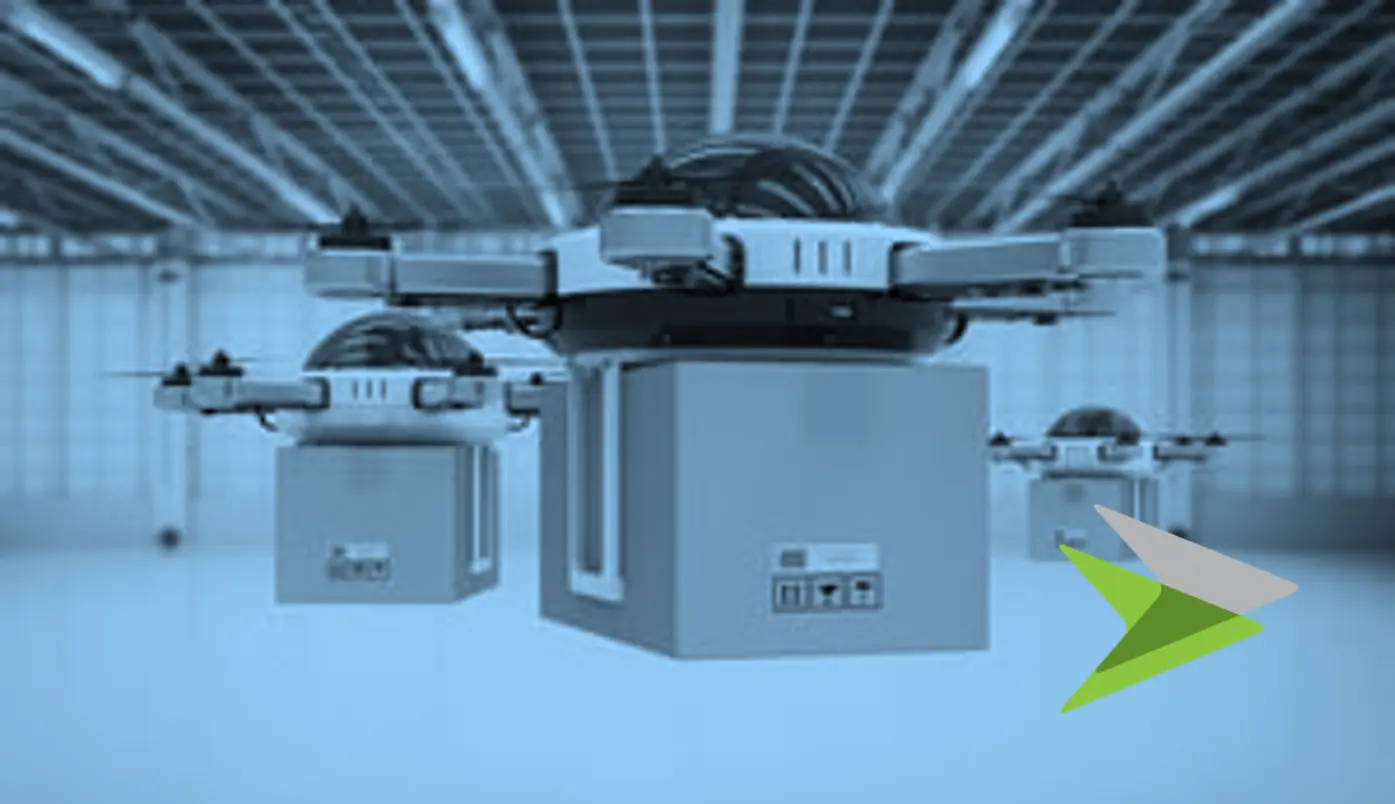
How Flying Drones Are Revolutionising Warehouses
It’s no longer a thing of the future – flying drones are now buzzing around our warehouses, and revolutionising the whole process. Whereas, not that
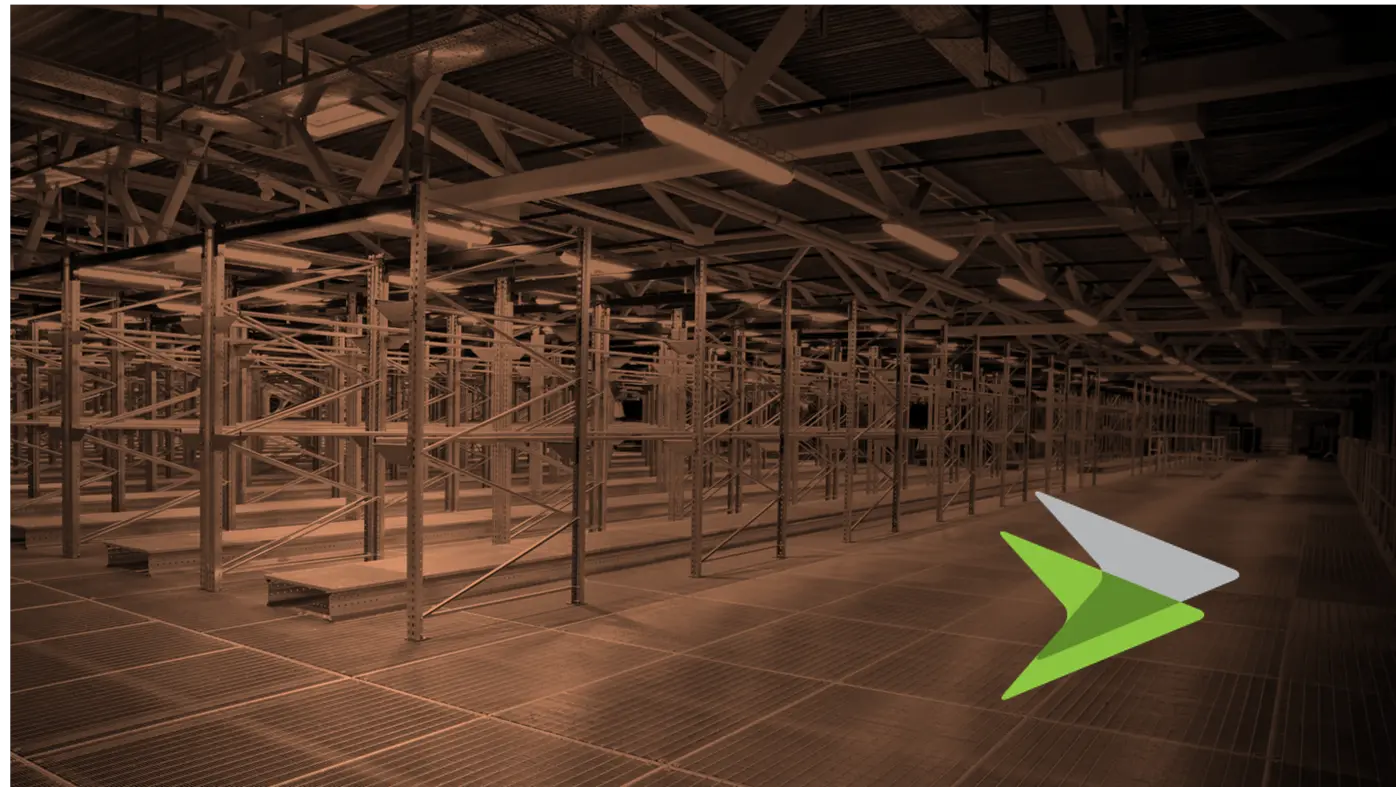
Warehouse Technologies on the Rise
With consumer service demands increasing and omni-channel operations becoming the fulfilment benchmark, development in warehouse technology is very much on the rise. Here’s a look
TESTIMONIALS
Client testimonials
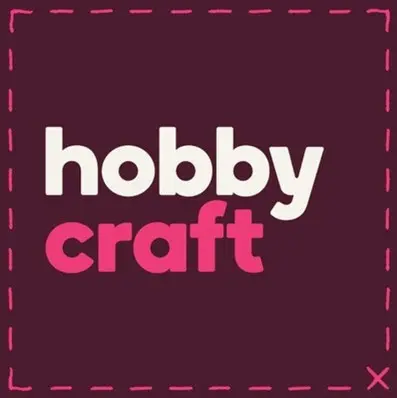
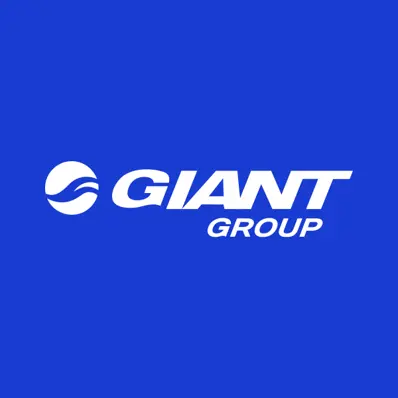
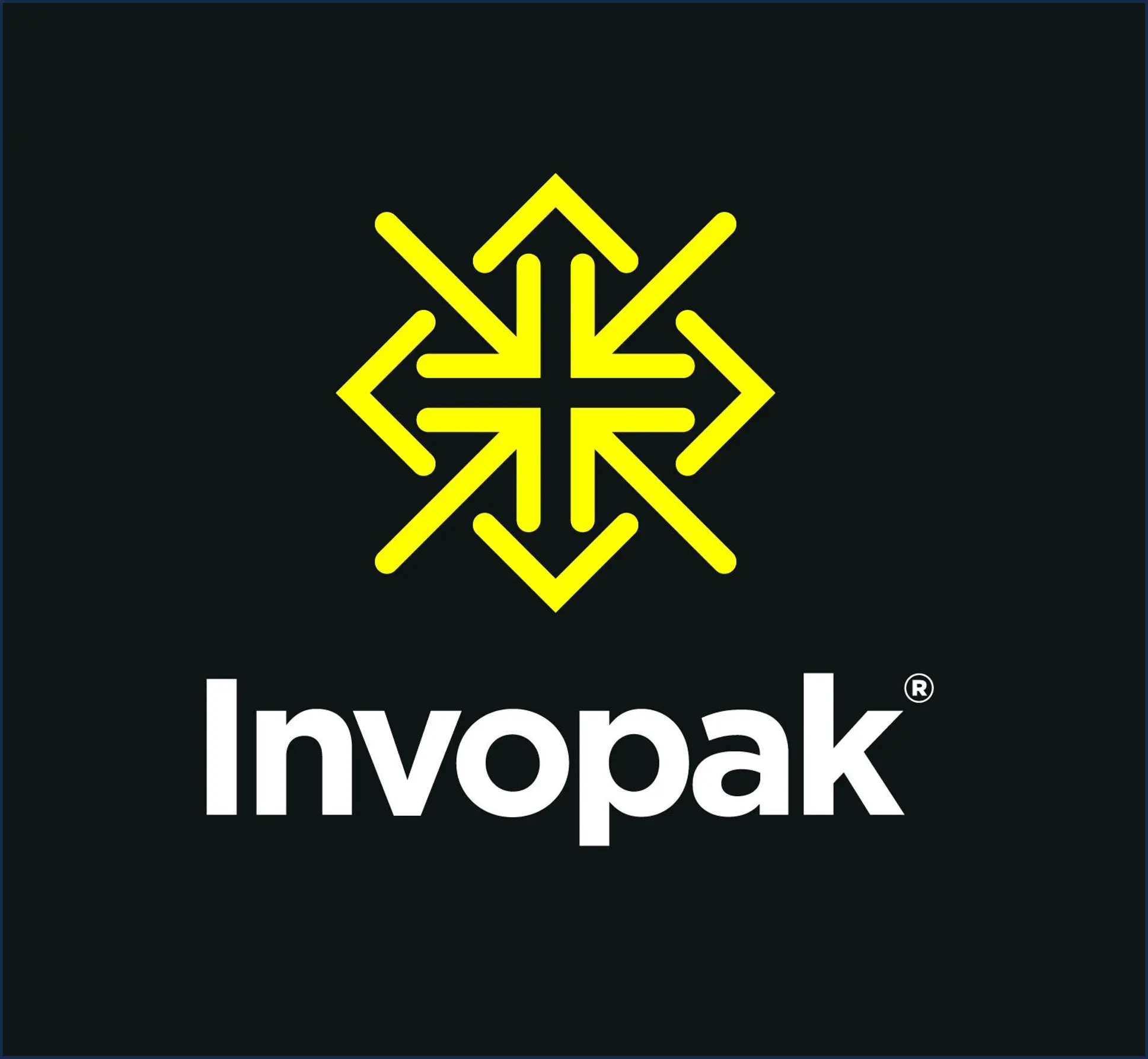
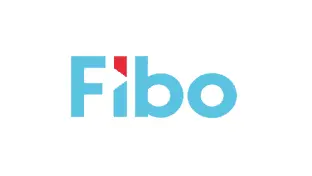
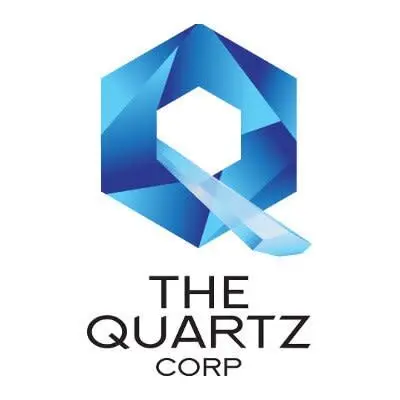
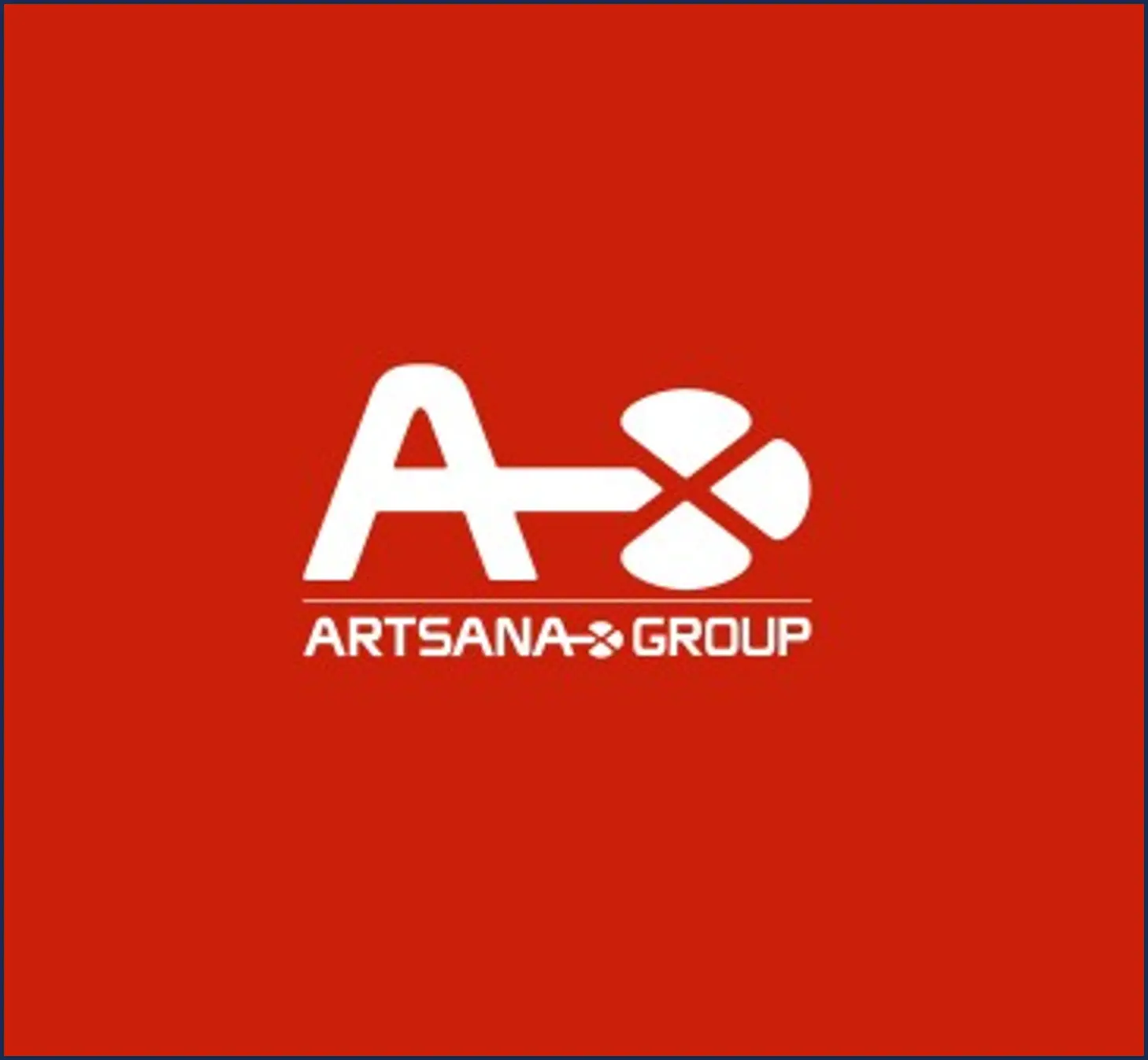
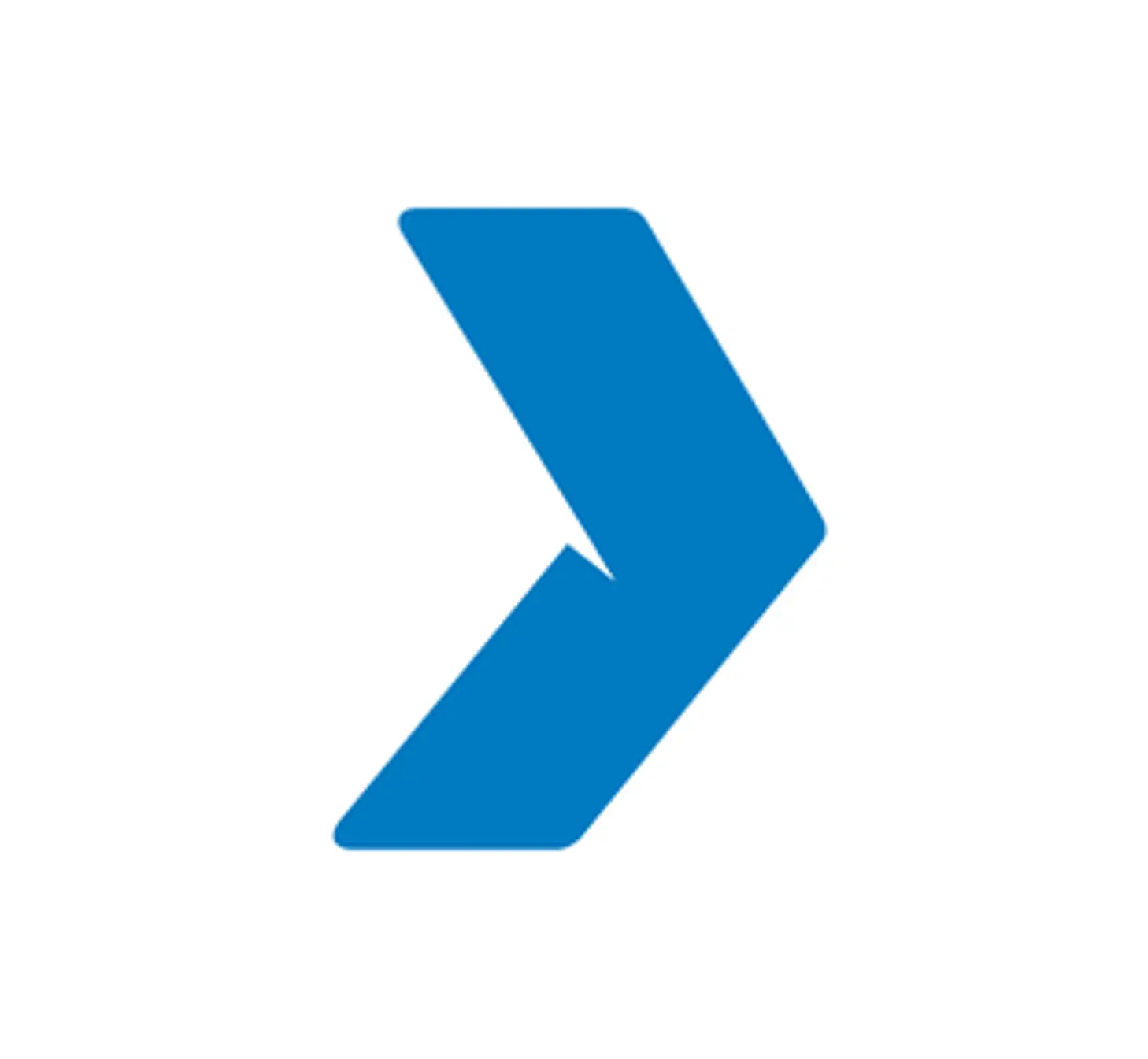